5 steps to make a better reinforcement plan for a construction project
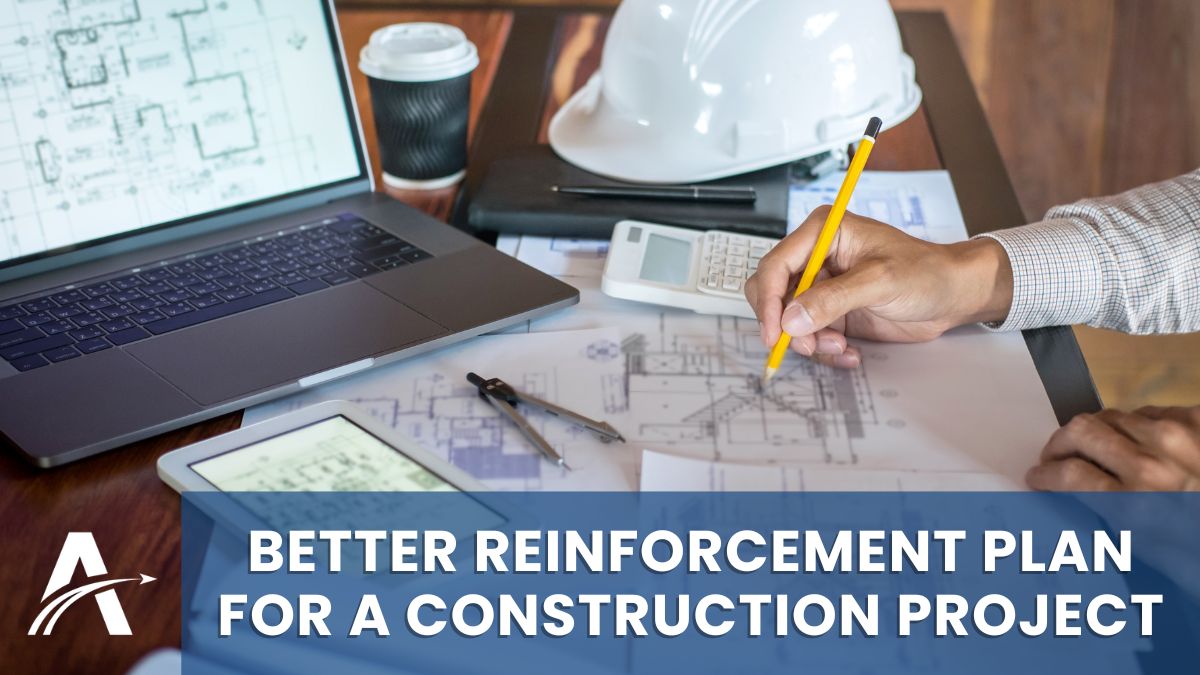
Creating an effective reinforcement plan for a construction project involves several key steps. Here’s a streamlined guide to help improve your reinforcement planning.
Step 1: Understand the Project Requirements
Review Structural Drawings and Specifications: Carefully analyze the structural drawings and specifications to understand the requirements for reinforcement, including the types, sizes, and placement of rebar.
- Contracts and Agreements: Examine all contractual documents to understand the scope of work, responsibilities, timelines, and financial aspects.
- Architectural and Engineering Drawings: Analyze detailed drawings to understand the design, dimensions, and specifications of the construction.
- Specifications and Standards: Review specifications to ensure that the materials, workmanship, and methods comply with industry standards and project requirements.
Site Assessment Data:
- Topographical Surveys: Review surveys to understand the site’s physical features, elevations, and potential challenges related to the terrain.
- Geotechnical Reports: Analyze soil testing reports to assess soil properties, stability, and suitability for construction.
- Environmental Impact Assessments: Examine reports to identify environmental considerations, such as protected areas, water sources, and potential hazards.
Regulatory and Compliance Information:
- Building Codes and Permits: Ensure that the project complies with local building codes and obtain all necessary permits and approvals.
- Safety Regulations: Review safety requirements and guidelines to ensure that the project meets occupational health and safety standards.
Stakeholder Requirements:
- Client Objectives and Expectations: Understand the client’s goals, priorities, and specific requirements for the project.
- Community and Stakeholder Input: Consider
Step 2: Consultation with Engineers
Consultation with engineers within construction projects is a critical process that ensures technical accuracy, feasibility, and alignment with design specifications. This collaboration involves various types of engineers (structural, civil, mechanical, electrical, etc.) and occurs at multiple stages of the project.
- Clear Communication: Ensure clear and open communication channels between all parties. Use project management tools to track discussions and decisions.
- Collaborative Tools: Utilize collaborative design and project management software to share documents, track progress, and facilitate real-time collaboration.
- Regular Updates: Keep all stakeholders informed with regular updates and progress reports to maintain alignment and transparency.
- Proactive Problem-Solving: Encourage a proactive approach to problem-solving, where potential issues are identified and addressed early through collaborative efforts.
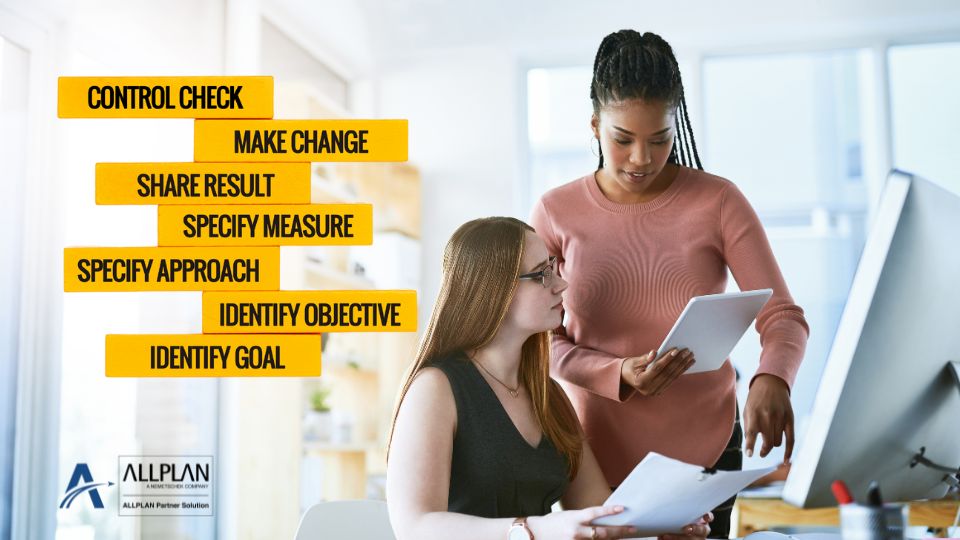
Step 3: Conflict resolution
Conflict resolution with engineers in a construction project is essential for maintaining progress and ensuring the project’s success. Here are some steps and best practices to effectively resolve conflicts with engineers:
- Clear Documentation: Keep detailed records of all communications, decisions, and actions related to the conflict resolution process. This ensures transparency and accountability.
- Active Listening: Practice active listening to fully understand the concerns and perspectives of all parties involved.
- Neutral Mediation: If necessary, involve a neutral third party to mediate the conflict and facilitate a fair resolution.
- Focus on Interests, Not Positions: Encourage parties to focus on their underlying interests and needs rather than fixed positions or demands.
- Respect and Professionalism: Maintain a respectful and professional demeanor throughout the conflict resolution process, avoiding personal attacks or blame.
- Training and Development: Provide training for team members on conflict resolution techniques and effective communication skills.
Step 4: Activity Planning
Develop a Clear Execution Plan: Outline the steps for placing and securing the rebar, including timelines, personnel responsibilities, and equipment needed.
Initial Meetings and Briefings:
- Kick-off Meetings: Organize initial meetings to introduce the project, its objectives, and scope to all engineering teams.
- Design Workshops: Conduct workshops to brainstorm and develop initial design concepts, ensuring all engineering disciplines contribute their expertise.
Document Review and Feedback:
- Blueprint and Specification Review: Engineers review architectural blueprints, structural designs, and technical specifications to provide feedback on feasibility and potential issues.
- Value Engineering: Engage in value engineering sessions where engineers suggest alternative solutions or materials that could reduce costs without compromising quality.
Detailed Design and Pre-Construction Phase
Technical Coordination:
- Regular Coordination Meetings: Hold regular meetings to discuss progress, resolve design conflicts, and coordinate between different engineering disciplines.
- Detailed Drawings and Calculations: Engineers develop detailed drawings, calculations, and technical documentation required for construction.
Peer Reviews and Approvals:
- Internal Reviews: Engineers perform internal peer reviews to ensure the accuracy and completeness of their designs.
- Client and Regulatory Approvals: Facilitate consultations to address client concerns and obtain necessary approvals from regulatory bodies.
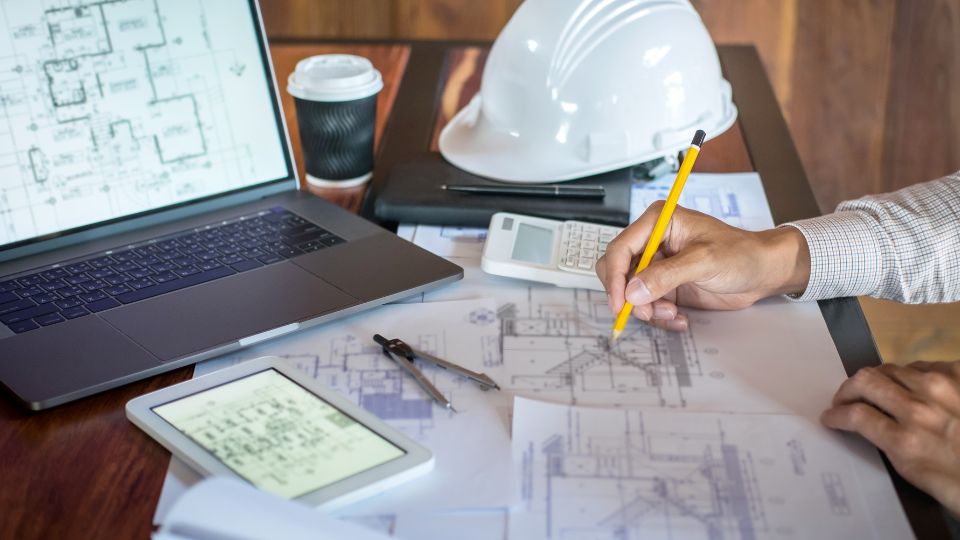
Construction Phase
Site Inspections and Adjustments:
- Pre-Construction Meetings: Engineers meet on-site to review construction plans and address any last-minute changes or site-specific issues.
- Regular Site Visits: Engineers conduct regular site visits to inspect ongoing work, ensure adherence to design specifications, and address any emerging issues.
Problem-Solving and Modifications:
- Technical Support: Provide ongoing technical support to the construction team, offering solutions to unforeseen challenges or design modifications.
- Design Adjustments: Make necessary adjustments to designs based on site conditions, material availability, or other factors.
Step 5: Final Verification
Engage a second person for a fresh perspective during the final review of the reinforcement plan. This external check ensures thoroughness, adherence to instructions, and overall accuracy.
- Conduct Regular Inspections: Perform regular inspections during the reinforcement installation to ensure compliance with the design and identify any issues early.
- Use Non-Destructive Testing (NDT): Implement NDT methods, such as ultrasonic testing or radiography, to check the integrity of the rebar without damaging the structure.
- Document and Report: Keep detailed records of inspections, test results, and any corrective actions taken. Provide regular reports to project stakeholders to ensure transparency and accountability.
By following these steps, you can enhance the effectiveness and reliability of your reinforcement plan, ensuring a robust and durable construction project.
More Posts
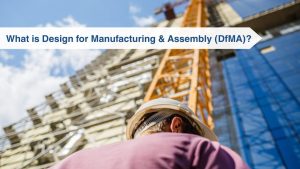
What is Design for Manufacturing and Assembly (DFMA)?
Source: Internet Design for Manufacturing and Assembly (DFMA) is a product design approach that focuses on simplifying the manufacturing and assembly processes to reduce production
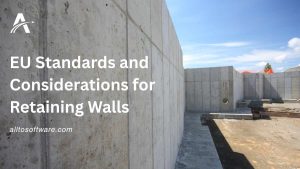
EU Standards and Considerations for Retaining Walls
Source: Internet A retaining wall is a structure designed to hold back or retain soil, rock, or other materials behind it. It is commonly used
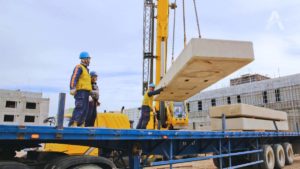
What Will the Prefabrication Trend Bring in 2025?
What Will the Prefabrication Trend Bring in 2025?